فرآوری سرباره کوره قوس الکتریکی
میزان تولید سرباره در یک کوره قوس الکتریکی با شارژ آهن اسفنجی به طور میانگین 350-300 کیلوگرم به ازای تولید هر تن فولاد است. لذا سالیانه حدود 8 میلیون تن سرباره در کشور تولید می-شود و مطابق با پیشبینی صورت گرفته در رابطه با تحقق تولید 55 میلیون تن فولاد برای سال 1404، به حدود 15 میلیون تن در سال افزایش خواهد یافت. در حال حاضر اکثر شرکتهای تولیدکننده آهن و فولاد، سرباره تولیدی خود را دپو میکنند و تاکنون راهکار فنی و اقتصادی مناسبی برای مدیریت این پسماند صنعتی وجود نداشته است. اما در حقیقت خصوصیات فیزیکی و شیمیایی سرباره در کنار مسائل زیستمحیطی، این پسماند را به یک ماده ارزشمند و دارای پتانسیل جهت بازیافت و استفاده مجدد تبدیل کرده است.
به طور کلی طراحی اصلی کورههای قوس الکتریکی در دنیا بر اساس شارژ قراضه آهن میباشد اما در ایران بهواسطه فراوانی منابع گاز طبیعی، فرآیند فولادسازی بر اساس تولید آهن اسفنجی به روش میدرکس و استفاده از آن به عنوان شارژ کوره قوس الکتریکی است. این امر سبب شده تا ماهیت فیزیکی و شیمیایی سربارههای داخل کشور با سایر سربارههای دنیا متفاوت باشد و یکی از دلایل اصلی که تاکنون راهحلی برای معضل دپو سربارهها در داخل کشور ارائه نشده، همین امر میباشد. این تفاوت سبب شده تا رفتار سربارههای ایران با سایر سربارههای تولید شده در دنیا متفاوت باشد و لذا این تفاوت بر کاربرد آن نیز تا حد بسیار زیادی اثرگذار است.
در راستای حل معضل دپو سربارهها در کشور، تیم تخصصی شرکت دانشبنیان صنایع معدنی راشا با تکیه بر بیش از 2 سال تجربه کار تخصصی در زمینه فرآوری سرباره کورههای قوس الکتریکی، اقدام به طراحی یک خط فناورانه جهت فرآوری سرباره نموده است. علاوه بر استحصال محصولات با ارزش از سرباره به نحوی که احداث خط فرآوری از نظر اقتصادی مقرون به صرفه باشد، یافتن کاربردی مناسب جهت حل معضل دپو سربارهها امری حائذ اهمیت است. در واقع بواسطه اینکه ایران در رتبه دهم تولید فولاد دنیا قرار دارد و علاوه بر دپوهای موجود فعلی، سالیانه حجم بالایی از آن تولید میشود، لذا در راستای حل مشکل دپوهای سرباره میبایست به دنبال کاربردی با قابلیت پوششدهی این حجم عظیم بود.
مطابق با پژوهشهای معتبر بینالمللی اعم از مقالات، پتنتها، گزارشات فنی و ...، کاربرد سرباره عمدتاً به عنوان جایگزین مواد تودهای در جادهسازی (به عنوان سنگدانه اساس و زیراساس و سنگدانه آسفالت) و در صنعت ساختوساز (به عنوان سنگدانه بتن و یا تولید سیمان) بوده است. اما باتوجه به اینکه سربارههای ایران دارای مقادیر بالای فازهای آهندار هستند، چگالی آنها نسبت به سنگدانههای طبیعی بالاتر است و لذا تولید بتن را با محدویت مواجه میکند و تنها میتوان از آن برای تولید بتن سنگین استفاده نمود که کاربرد بسیار محدودی دارد. از سوی دیگر چگالی بالاتر سرباره سبب افزایش هزینه حمل و نقل آن برای جادهسازی خواهد بود و در بسیاری از مواقع به دلیل عدم ارزش اقتصادی بالای سنگدانههای طبیعی (از جنس شن و ماسه) و وفور معادن شن و ماسه در کشور، حمل سرباره و کاربرد آن در جادهسازی (به عنوان جایگزین سنگدانه اساس و زیراساس و یا سنگدانه آسفالت) منطقی و اقتصادی نیست. از سوی دیگر بکارگیری سرباره در صنعت سیمان به دلیل ظرفیت تولید بسیار بالای سیمان در کشور (حدود 60 میلیون تن) از جمله کاربردهای پرپتانسیل میباشد که حجم مصرف سرباره در آن بالاست اما باتوجه به محتوای بالای آهن در سربارههای ایران، امکان استفاده از آن در صنعت سیمان با مشکل مواجه خواهد شد.
بررسی اغلب سربارهها نشان داده است که عمده فازهای موجود در سرباره، فازهای کلسیم سیلیکاتی و اکسید آهن دو ظرفیتی بنام وستیت (FeO) بوده که این فاز FeOعمدتاً در ترکیب با MgO و MnO به صورت محلول جامدی با نام فاز RO، میباشد. همچنین بخشی از آهن موجود در سرباره به صورت آهن فلزی وجود دارد. لذا طراحی مطلوب یک مدار فرآوری میبایست به گونهای انجام میشد که علاوه بر قابلیت جداسازی فازهای آهندار (آهن فلزی و ذرات آهن اکسیدی) به صورت حداکثری، امکان استفاده از باطله باقیمانده را نیز ایجاد کند زیرا در صورتی که نتوان ذرات آهن فلزی را به طور کامل حذف و فازهای اکسید آهن را به حداقل رسانید، بکارگیری باطله برجای مانده در صنعت سیمان مسیر نخواهد بود.
بدلیل اینکه کاربرد اصلی در نظر گرفته شده برای ذرات تودهای سرباره، استفاده به عنوان جایگزین کلینکر در تولید سیمان است، مدار فرآوری مناسب برای بازیافت سرباره کوره قوس الکتریکی به صورت خشک طراحی شده تا ضمن عدم نیاز به خشک شدن ذرات سرباره، از مصرف آب که امروزه کمبود آن خود مشکلی بزرگی است، خودداری شود. این مدار فرآوری شامل 14 مرحله اصلی بوده که خوراک سرباره اولیه طی پیمودن این مراحل به چهار محصول نهایی تبدیل میشود:
1- قراضه درشت آهنی تمیز شده مناسب شارژ مجدد در کوره قوس الکتریکی (به میزان حدود 5/1-1 درصد وزنی)
2- ذرات آهن فلزی تمیز با خلوص بالای 98% با قابلیت تبدیل به بریکت و شارژ مجدد کوره (به میزان حدود 5-2 درصد وزنی)
3- کنسانتره با محتوای آهن کل در محدوده 45 الی 65 درصد با قابلیت فروش (به میزان 6-3 درصد وزنی)
4- مواد تودهای فاقد آهن فلزی و با حداقل فازهای آهن¬دار مناسب صنعت سیمان در ابعاد زیر 3 میلیمتر (به میزان 94-90 درصد وزنی)
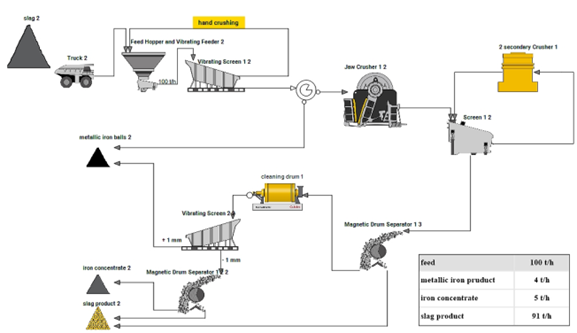
شماتیک ساده از مدار فرآوری طراحی شده برای سرباره کوره قوس الکتریکی
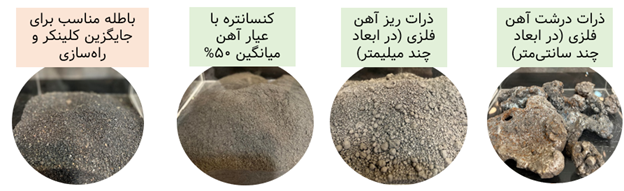
تصویر محصولات خط فناورانه فرآوری سرباره شرکت راشا
استحصال سه محصول شماره 1 تا 3، ارزش اقتصادی خط فرآوری را تضمین میکند و باطله برجای مانده به راحتی قابلیت جایگزینی تا 15% درصد وزنی با کلینکر در تولید سیمان تیپ 2 را دارد. تولید کلینکر اصلیترین مرحله تولید سیمان پرتلند میباشد زیرا با افزودن حدود 10 درصد سنگ گچ به کلینکر، سیمان پرتلند تولید خواهد شد. مصرف انرژی (خصوصاً گاز طبیعی) در فرآیند تولید سیمان بسیار بالاست به گونهای که حدود 7% آلایندگی صنعت را به خود اختصاص داده است. همچنین در فصل زمستان به دلیل مشکلات قطعی گاز، بسیاری از این کارخانهها توان تولید با حداکثر ظرفیت خود را ندارند. در فرآیند تولید سیمان، بیشترین مصرف انرژی در کوره پخت دوار کلینکر انجام می-شود. بنابراین درصورتی که یک کارخانه سیمان از سرباره به عنوان جایگزین بخشی از کلینکر تولیدی خود استفاده کند، مصرف انرژی خود و به تبع آن هزینههای تولید سیمان آن کاهش مییابد. همچنین استفاده از سرباره بدلیل وجود مقادیر اکسید آهن بالا، سبب تیرهتر شدن رنگ نهایی سیمان تولید شده میشود و طبق مذاکرات انجام شده با این کارخانهها، مشتری پسندتر میباشد. لذا علاوه بر مشخصات مناسب باطله برجای مانده به عنوان جایگزین کلینکر، از نظر کارخانههای تولید سیمان نیز بنا به دلایل مذکور و طبق مذاکرات انجام شده با آنها، استفاده از سرباره به عنوان جایگزین بخشی از کلینکر در این کارخانهها بسیار جذاب است.